ROBOTIC MULTI-ARM SOLUTIONS FOR SHOT BLASTING REEFER CONTAINERS
Clemco Denmark's robotic multi-arm solutions for shot blasting featuring up to four synchronized robots that blast in parallel and has a magnificent blasting cleaning and surface preparation coverage.
Advantages of Using Multi-Arm Robotic Solutions for Shot Blasting reefer containers
Our multi-arm robotic solution is designed for shot blasting large and complex surfaces, like reefer containers, ensuring precise, efficient, and uniform treatment. With up to four synchronized robotic arms, this solution offers enhanced access to intricate and hard-to-reach areas, delivering consistent performance with speed and accuracy.
By utilizing our multi-arm robotic solution for shot blasting, companies can achieve superior surface preparation, enhanced productivity, and improved safety while ensuring high-quality results for reefer containers.
Check out the advantages listed below:
Enhanced Access to Complex and Large Surfaces
- Multi-arm technology provides superior reach, ensuring complete surface coverage, even on large and intricate container geometries.
- Ideal for reefer containers and similar structures with challenging angles and designs.
Fast and Precise Shot Blasting
- Up to four synchronized robotic arms work simultaneously, drastically reducing process time while maintaining high precision.
- Ensures uniform abrasive flow, delivering consistent and effective blasting results.
Consistent and Uniform Treatment
- The synchronized control system ensures even abrasive distribution across all surfaces, eliminating inconsistencies often found with manual processes.
- Maintains consistent treatment quality, improving coating adhesion and corrosion resistance.
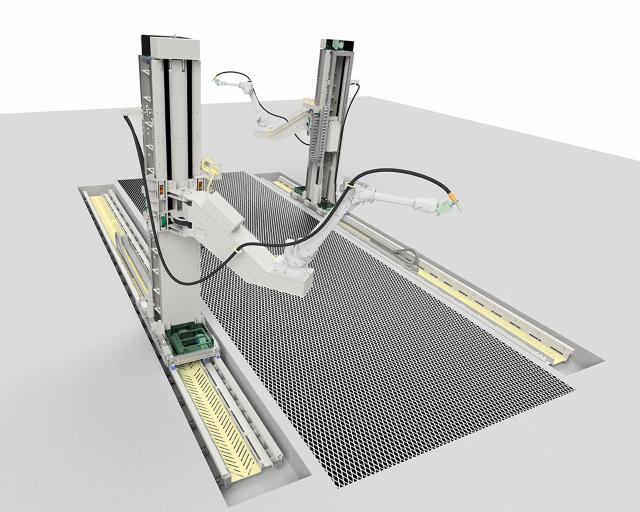
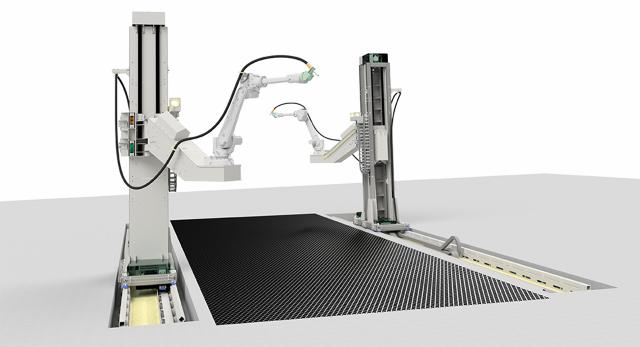
Optimized Production Efficiency
- Automated movement and intelligent blasting patterns reduce manual labor, speeding up the production process.
- Enhances throughput and optimizes the use of blasting materials, reducing waste and cost.
Improved Surface Preparation Quality
- Delivers a thorough, high-quality shot blasting finish that prepares surfaces for optimal anti-corrosion treatments.
- Provides the precise roughness and cleanliness required for coating adhesion.
Increased Safety and Automation
- Fully automated solution reduces the need for workers to operate in hazardous environments, improving workplace safety.
- Minimizes human error, ensuring repeatable and reliable results.
Adaptability for Various Container Sizes
- The multi-arm system can be easily adjusted to handle different container sizes and shapes, offering flexibility in production.
- Seamlessly integrates into existing production lines with minimal disruption.
Robotic Features
Our advanced multi-arm robotic solution for shot blasting reefer containers is engineered for high-precision surface preparation, ensuring optimal adhesion for subsequent coatings and anti-corrosion treatments. Equipped with up to four synchronized industrial robotic arms, the system delivers consistent and efficient shot blasting, even on complex container geometries.
The robotic arms are integrated with advanced motion control and real-time process monitoring, ensuring uniform blasting coverage while maintaining precise abrasive flow rates. Operating on external axes, the system enables full surface reach, eliminating inconsistencies and optimizing material usage.
With offline trajectory planning and adaptive programming, the solution adjusts dynamically to different container sizes and structures, providing repeatable, high-quality results. The system’s modular design allows for seamless integration into existing production lines, enhancing throughput while reducing manual labor requirements.
Designed for continuous operation in demanding industrial environments, the solution features automated nozzle adjustments and intelligent abrasive recycling systems to maximize efficiency and minimize waste. By improving blasting accuracy and reducing process time, our robotic multi-arm solution significantly enhances productivity, safety, and coating adhesion for reefer containers.
Built for durability, the system is capable of operating continuously in demanding industrial environments with minimal maintenance. Its modular and adaptable design accommodates steel structures of varying sizes and shapes, providing flexibility for diverse surface treatment requirements. The enclosed blasting environment supports efficient abrasive recycling, reducing waste and enhancing sustainability. This cutting-edge solution ensures the highest standards of performance, making it ideal for preparing steel components for anti-corrosion coatings.
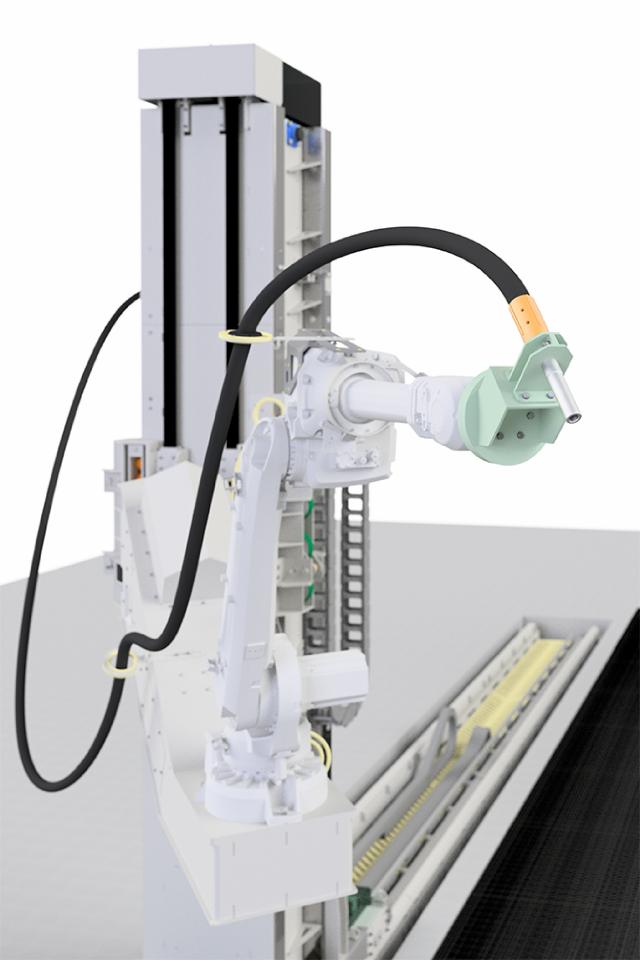
GET IN TOUCH WITH OUR EXPERTS
If you want to learn more about how our advanced multi-arm robotic solution can optimize the shot blasting process for reefer containers, our team of experts is ready to assist you. Engineered for precise, efficient, and uniform surface preparation, this system ensures optimal adhesion for subsequent anti-corrosion treatments while delivering consistent coverage, even on complex container structures.
Get in touch with us today to explore how our multi-arm technology enhances process efficiency, improves blasting consistency, and reduces abrasive consumption. Let us help you elevate your surface treatment operations with innovative, high-performance robotic solutions.

From delivery to production
Installation and commisioning
Our site supervisors are responsible for installation in close collaboration with the engineering team and the customer’s team on site. By using our own supervisors, we ensure that the installation is carried out according to the design drawings and the in-house quality tests.
We set up the complete process line and supervise all installation tasks. We have the necessary insurance and permits for the installation of epoxy and polyurethane systems and are able to accommodate most HSSE requirements during the work. In addition, we offer a full CE approval of the entire solution.
Full documentation package
When our technical department develops technical solutions for our customers, the documentation package is just as important as the actual product.
The documentation package is performed according to the standards and certifications applicable for the specific product or country.
Service and maintenance
Clemco Denmark has a highly skilled service department with experts in surface treatment equipment and robotic solutions. Part of our documentation package is delivering a complete spare part lists and expected life spans on consumable parts that are included in the service program. We guarantee that spare parts are available during a certain lifetime. In addition, Clemco Denmark provides personal protective equipment for operators, and we have a large inventory of different spare parts.
Training of operating personnel
Part of commissioning is training the operators and technicians in operating the robotic system. We also carry out training in correct maintenance of the installation and replacement of key components.
We introduce the individual procedures to respect the agreed transfer efficiency rates and process time. It is an essential part of our project management that a thorough hand-over of the system is carried through.