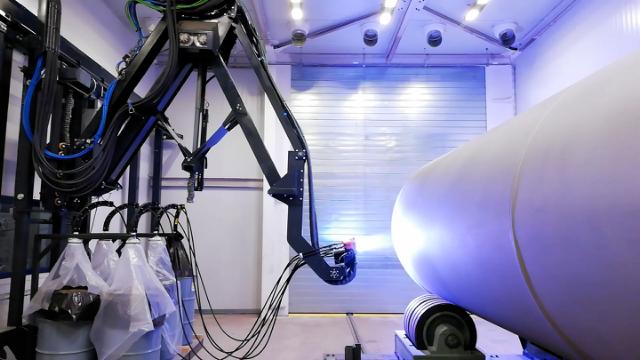
Surface treatment with or without robot
At Clemco Denmark we are experts in surface treatment both with and without automation. This enables us to guide our customers to the optimal solution, and to advice when a robotic solution is better suited for your surface treatment processes.
Advantages of using robots for protective coating
- Quality improvement by accurate controlling of materials
- Improvement of working environment
- Better cost efficiency - an industrial robot is not as expensive as many people think
- Optimization of production time
- Consistent surface quality
- Savings in energy
- Savings in material consumption
- Less masking needed
- Less exposure for materials that are harmful to health
- Robotic solutions do not mind long working hours
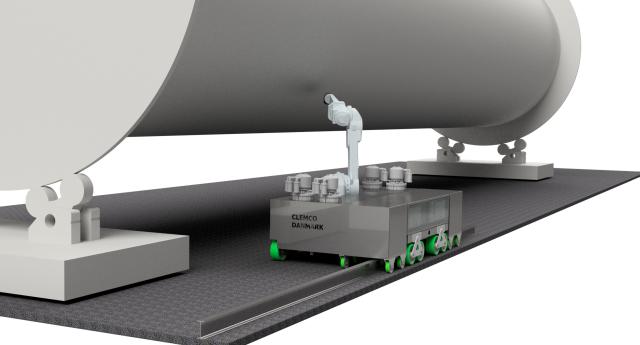
Quality improvements when using robotic solutions
For repetitive surface treatment jobs, robots may be superior compared to human operators in terms of the uniformity when it comes to shotblasting, metallization or the sprypainting work that is produced.
When chosing a robot to do the surface cleaning one or more of the following improvements will be obtained:
- High positioning precision of the steel surface in relationship to the gun or nozzle
- High repeatability and transport of parts on line tracking conveyors
- No deviation due to fatigue or other human related spray patterns
- Highly accurate inspection and measurement using in-situ DFT measurements etc.
These process improvements not only improve the visual appearance of a surface coating job, but also better overlaps are achieved due to the tighter control of the gun angle and controlled distance from the spray or nozzle tip to the surface to be coated.
For what concerns zinc spray metallization and spray painting, robotic solutions improve the layer thickness consistency, but it also gives a major saving in consumption of materials and therefore also a great saving in costs. Similar improvements can be achieved for shot blasting as well as the robot is programmed to create a certain roughness with a certain kind of blast media.
Improvement of the working environment
With robotic automation you reduce fatigue and minimize the risk of injury, and with the increased health and safety legislation it is predicted that companies within surface treatment should consider automated processes.
- Robotic shot blasting eliminates the heavy work of controlling stiff blast hoses and the noisy and dusty work environment.
- Robotic metallizing replace the repetitive job of handling a heavy spray gun and eliminates the exposure to UV light and zinc dust.
- Robotic spray painting replaces fatiguing hand movements and reduces human exposure to dangerous VOC levels.
There are thus many possibilities to improve both the quality of the surface treatment, but also to improve the working conditions to which the operators are exposed.
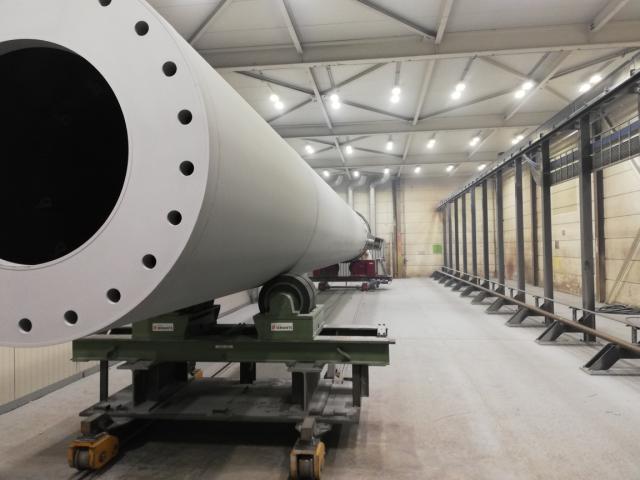
Cost savings using robotic surface processes
Our surface coating robots are able to operate continuously 24/7 in order to get the best productivity output. If they run on lines staffed and surveyed by human operators, we all know that this kind of work requires breaks now and then, which makes it difficult for the robots to run 24/7. Often it is the human operators in the process (DFT measurements etc.) who limit the output of a robot cell in surface coating. There is of course the natural savings; a robot is neither on the salery list nor does it need work breaks, but in the cost saving equation the benefit of the robot can be outlined like this:
- The life time of a standard industrial robot is at least 10 years when correctly maintained and protected.
- The robot requires less air ventilation and no heating of substituted air during the cold months of the year.
- The robot will perform a consistent coating job that will save blast media / paint / zinc wire all dependig what kind of istallation the robot is set up to do.
It is our experience that those previously employed people in coating operations are typically trained as process technicians who can perform program changes and optimization of the robotic coating processes.
The scribing process can be performed using off-line programming when the spray fan widths is proven. This reduces some of the programming work, but there is no 100% substitution for on-site programming.