ROBOTIC SOLUTIONS FOR METALLIZATION FOR TOWER SECTIONS AND MONOPILES
By adopting a robotic cart solution for metallizing tower sections and monopiles, companies can achieve significant operational improvements, elevate product quality, and enhance their competitiveness in the renewable energy and heavy steel manufacturing sectors.
Advantages of Metallizing Tower Sections and Monopiles Using a Robotic Cart Solution
The use of robotized arc metallization to apply zinc or zinc-aluminum coatings offers the advantage of achieving highly uniform coverage, which also streamlines quality control processes.
Metallizing large structures like wind tower sections and monopiles is a crucial process for enhancing their corrosion resistance, and overall performance in demanding environments. Implementing a robotic cart solution for this task brings a host of benefits compared to traditional manual or semi-automated methods.
Below you find the list of benefits when investing in a robotic solution from Clemco Denmark.
Improved Efficiency
- Robotic systems work consistently and continuously, reducing downtime and increasing throughput.
- The coating speed when using our robotic metallizing system is approximately 160 square meters per hour.
Enhanced Precision
- Robots ensure uniform application of coatings, resulting in consistent thickness and quality. This also leads to material reduction of zinc or zinc aluminum wires.
- Minimizes overspray and material wastage through precise control.
Superior Quality and Durability
- Improved coating uniformity ensures better protection against corrosion and wear.
- Reduces the likelihood of coating defects, improving the lifespan of the structures.
Scalability for Large Components
- Specifically designed to handle massive structures like wind tower sections and monopiles.
- Provides full coverage for large surfaces with complex geometries. The system can also bypass obstacles such as man holes.
Cost Efficiency
- Lower operational costs due to reduced material waste and faster processing times. Our experience is a high transfer efficiency and a general saving of minimum 15% in material compared to manual arc spraying application methods.
- Decreases labor costs by automating repetitive and time-consuming tasks.
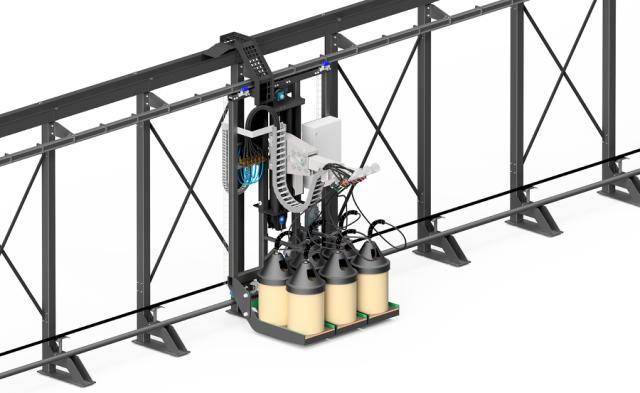
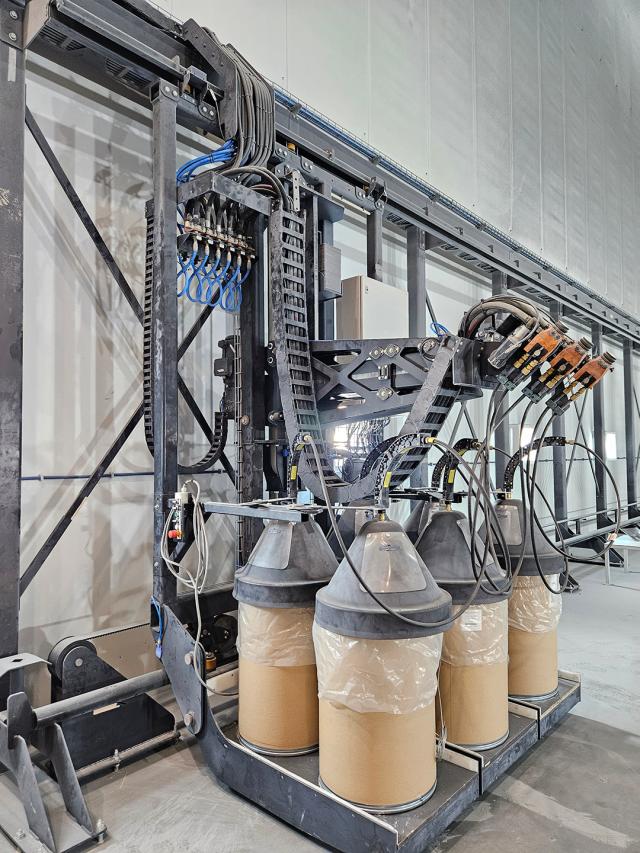
Enhanced Worker Safety
- Reduces human exposure to hazardous environments, such as the fumes and dust from the arc process.
- Minimizes physical strain and the risk of injuries associated with manual application.
Environmental Benefits
- Precise application minimizes environmental impact by reducing overspray and material wastage by a minimum of 15% compared to manual spraying applications.
- Supports sustainable practices with optimized resource usage.
Flexibility and Adaptability
- Robotic carts can be programmed to handle different sizes and conical shapes, adapting to various wind tower project requirements.
- Allows integration with other automation systems in production lines and data capture systems.
Data-Driven Insights
- Equipped with sensors and monitoring systems, it provides real-time feedback on process parameters such as amperage, wire consumption, and compressed air usage.
- Enables process optimization and quality control based on collected data.
Competitive Advantage
- Demonstrates innovation and technological leadership in the industry.
- Enhances the company’s reputation by delivering products of superior quality.
Robotic features
Our robotic cart solutions for metallizing monopiles and tower sections are engineered for precision and efficiency in handling large-scale structures.
The system features advanced robotic arms and adjustable carts, ensuring uniform coating application across cylindrical surfaces of varying diameters and lengths and conical geometries. Designed for durability, it operates seamlessly in the demanding environment with metallizing dust to provide a consistent performance with low maintenance.
The system can typically be programmed based on a set of tower parameters including length and tower diameters and the desired arc metallization layer thickness. The system can then detect a placed tower section using sensors and the robotic metallization work can be started by an operator directly from the control panel.
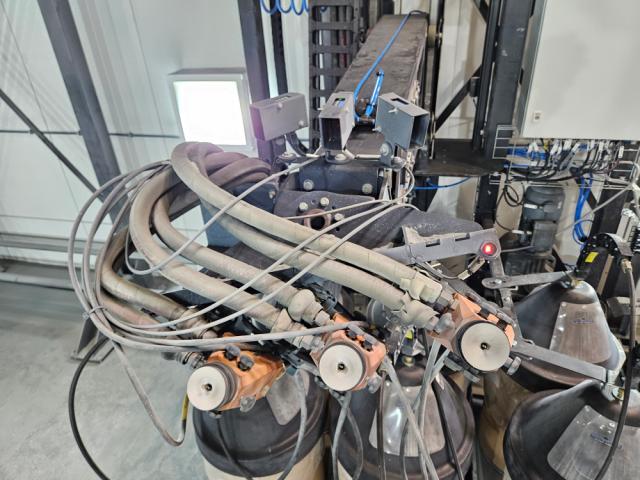
GET IN TOUCH WITH OUR EXPERTS
Maximizing efficiency in surface treatment booths requires innovative solutions, even in limited spaces. Our robotic cart systems for metallization are specifically designed to deliver outstanding performance while addressing spatial constraints.
If you are considering automating your production, we invite you to connect with us. Discover how Clemco Denmark can transform your surface treatment processes. Let us help you optimize operations, boost productivity, and maintain your competitive role in the wind industry.

FROM DELIVERY TO PRODUCTION
Installation and commisioning
Our site supervisors are responsible for installation in close collaboration with the engineering team and the customer’s team on site. By using our own supervisors, we ensure that the installation is carried out according to the design drawings and the in-house quality tests.
We set up the complete process line and supervise all installation tasks. We have the necessary insurance and permits for the installation of epoxy and polyurethane systems and are able to accommodate HSSE requirements during the work. In addition, we offer a full CE approval of our robotic solution.
Full documentation package
When our technical department develops technical solutions for our customers, the documentation package is just as important as the actual product.
The documentation package is performed according to the standards and certifications applicable for the specific product or country. The documentation package is also used to identify spare parts and consumables.
Service and maintenance
Clemco Denmark has a highly skilled service department with experts in surface treatment equipment and robotic solutions. Part of our documentation package is delivering a complete spare part lists and expected life spans on consumable parts that are included in the service program.
We guarantee that spare parts are available during a certain lifetime. In addition, Clemco Denmark provides personal protective equipment for operators, and we have a large inventory of different spare parts and consumables.
Training of operating personnel
Part of commissioning is training the operators and technicians in operating the robotic system. We also carry out training in correct maintenance of the installation and replacement of key components.
We introduce the individual procedures to respect the agreed transfer efficiency rates and process time. It is an essential part of our project management that a thorough hand-over of the system is performed.