ROBOTIC SOLUTIONS FOR SHOT BLASTING TOWER SECTIONS AND MONOPILES
By implementing a robotic cart solution for shot blasting tower sections and monopiles, companies can streamline surface preparation operations, improve surface preparation quality, and strengthen a competitive position in the renewable energy and heavy manufacturing industries.
Advantages of Shot Blasting Tower Sections and Monopiles Using a Robotic Cart Solution
Shot blasting is a critical step in preparing large structures like wind tower sections and monopiles, ensuring the surfaces are clean and ready for further treatments like metallization and spray painting. Utilizing a robotic cart solution for this process offers numerous advantages over traditional methods, enhancing efficiency, quality and safety.
By adopting robotic cart solutions for shot blasting, companies can achieve superior surface preparation, optimize production workflows, and strengthen their position in the renewable energy and heavy manufacturing sectors.
Enhanced Surface Preparation Quality
- Achieves consistent and uniform blasting across the entire surface, even on large cylindrical structures.
- Removes rust and scale effectively and is ensuring an optimal surface roughness profile for the next coatings and treatments.
Increased Efficiency
- Automates the blasting process, significantly reducing processing time for each component. A typical production output is 120 m2 per hour with two blasting nozzles at 8-9 bars blasting pressure.
- Operates continuously with minimal downtime, boosting overall productivity.
Adaptability for Large Structures
- Designed specifically for massive elements like monopiles and wind tower sections.
- Capable of handling different sizes and geometries with precise adjustments.
Cost Savings
- Reduces labor costs by automating a time-intensive manual task.
- Minimizes abrasive material waste through controlled application.
- Data can be retrieved for air flow and blast media consumption.
Improved Worker Safety
- Removes personnel from hazardous environments with high dust levels and flying debris.
- Reduces exposure to noise and vibration associated with manual blasting.
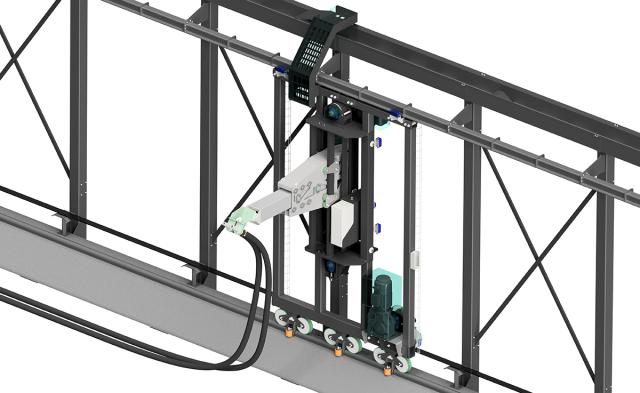
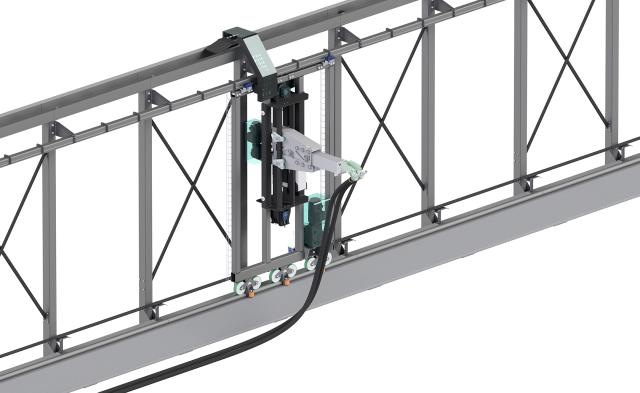
Reliability and Consistency
- Robotic systems deliver the same high-quality results repeatedly, eliminating inconsistencies associated with manual methods.
- Real-time monitoring ensures process parameters are maintained for optimal outcomes. Air flow and blast media consumption can be monitored in real time conditions.
Environmental Benefits
- Optimized abrasive usage decreases waste and environmental impact.
- Energy utilization is typically improved by a minimum of 30% due to blasting effciency and less over blasting.
Reduced Maintenance and Downtime
- Robust robotic systems are designed for durability and long-term use in demanding environments. Each component exposed to blasting media and recioil is protected for optimal life time in the very harsh environment.
- Regular automated calibration and diagnostics reduce the need for frequent manual maintenance.
Competitive Edge
- Demonstrates advanced technological capabilities, enhancing brand reputation.
- Supports increased throughput and superior product quality, meeting industry demands efficiently.
Robotic Features
Our robot solutions for shot blasting of wind turbine towers and monopiles are developed from a cart solution that drives the robot arm parallel to the tower section. This gives us a stable construction that can be loaded with blasting equipment in addition to the manipulator arm that performs the motions of the blasting process to the steel surface.
The system incorporates advanced robotic control and adjustable carts, enabling thorough and uniform blasting across cylindrical surfaces of varying diameters and lengths. The robot arm can be set for different sizes of tower section sizes and with adjustment of blasting parameters directly on an HMI touch screen where already created programs can also be recalled from.
Integrated sensors and real-time process monitoring optimize blasting parameters, ensuring efficient material usage while maintaining surface preparation standards.
One of the advantages of our robotic systems is that all axes can be set up independently of each other, making the complexity of programming very simple for operators to understand. It takes about 30 minutes to perform a complete program for robotic shot blasting of a full size wind tower section.
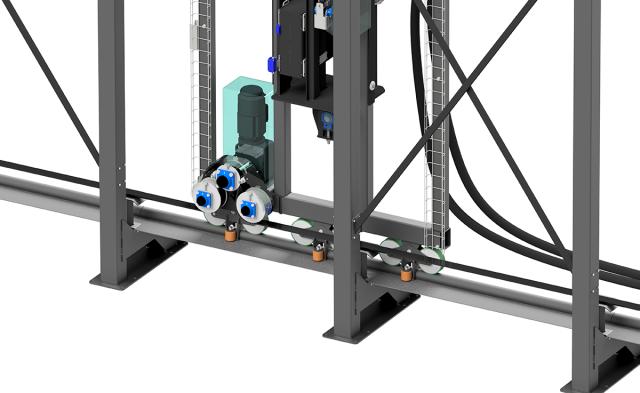
GET IN TOUCH WITH OUR EXPERTS
Maximizing efficiency in shot blasting processes is required when surface cleaning tower sections and monopiles. Our robotic cart systems for shot blasting are engineered to deliver exceptional performance, even when working with massive tower sections in limited spaces.
If you're looking to automate and enhance your production, we invite you to reach out to us. Discover how Clemco Denmark's innovative solutions can revolutionize your shot blasting processes, streamline operations, and give you a competitive edge in the wind industry. Let's make your production smarter, faster, and more efficient together!
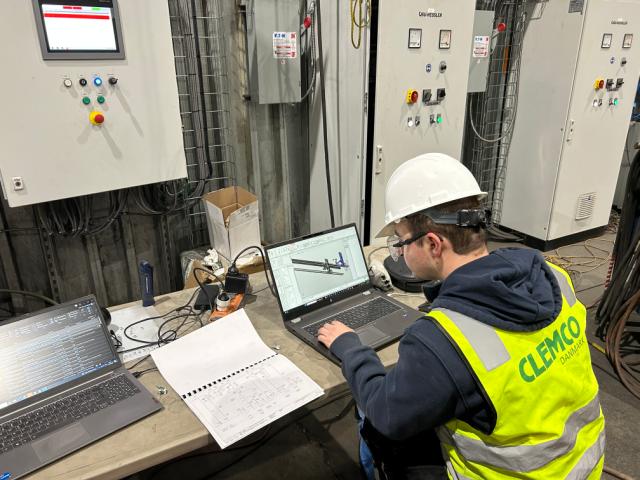
From delivery to production
Installation and commisioning
Our site supervisors are responsible for installation in close collaboration with the engineering team and the customer’s team on site. By using our own supervisors, we ensure that the installation is carried out according to the design drawings and the in-house quality tests.
We set up the complete process line and supervise all installation tasks. We have the necessary insurance and permits for the installation of epoxy and polyurethane systems and are able to accommodate most HSSE requirements during the work. In addition, we offer a full CE approval of the entire solution.
Full documentation package
When our technical department develops technical solutions for our customers, the documentation package is just as important as the actual product.
The documentation package is performed according to the standards and certifications applicable for the specific product or country. It is a prerequisite for CE-marking of the machine, and a great tool for our engineers and site managers to use, when advising customers on site or remotely from our office in Skanderborg.
Service and maintenance
Clemco Denmark has a highly skilled service department with experts in surface treatment equipment and robotic solutions. Part of our documentation package is delivering a complete spare part lists and expected life spans on consumable parts that are included in the service program.
We guarantee that spare parts are available during a certain lifetime. In addition, Clemco Denmark provides personal protective equipment for operators, and we have a large inventory of different spare parts.
Training of operating personnel
Part of commissioning is training the operators and technicians in operating the robotic system. We also carry out training in correct maintenance of the installation and replacement of key components.
We introduce the individual procedures to respect the agreed transfer efficiency rates and process time. It is an essential part of our project management that a thorough hand-over of the system is carried through.